FDC 와 SPC
FDC와 SPC는 반도체, 디스플레이, 정밀 제조 공정에서 공정 품질 관리 및 이상 감지를 위해 사용되는 핵심 기술입니다.
1. FDC (Fault Detection and Classification)
목적
- 공정 장비 및 제조 공정에서 발생하는 이상 현상(Fault)을 감지하고 원인을 분류(Classification)하는 시스템
- 주로 반도체, 디스플레이, 정밀 제조 공정에서 활용됨
주요 기능
- 실시간 데이터 모니터링
- 센서에서 온도, 압력, 전류, 가스 흐름 등의 데이터를 실시간으로 수집
- 이상 감지 (Fault Detection)
- 정상 공정 패턴과 비교하여 이상 징후가 발생하면 경고 발생
- 이상 원인 분석 (Classification & Root Cause Analysis)
- 머신러닝, 통계 기법 등을 이용하여 이상 발생 원인 분석
- 공정 최적화
- 반복적인 이상 발생 시 공정 개선을 위한 피드백 제공
적용 예
- 반도체 제조 공정에서 PECVD(Plasma Enhanced Chemical Vapor Deposition) 장비의 온도 변화 이상 감지
- 웨이퍼 가공 중 챔버 내 압력 이상 감지 및 원인 분석
- 챔버(Chamber)는 반도체, 디스플레이, 정밀 제조 공정에서 진공, 가스, 플라즈마 등의 환경을 조성하여 특정 공정을 수행하는 밀폐된 공간입니다.
2. SPC (Statistical Process Control, 통계적 공정 관리)
목적
- 제조 공정에서 통계적 기법을 이용하여 품질을 관리하고 변동을 최소화
- 제어 한계(Control Limits)를 설정하여 이상 여부를 판단
주요 기능
- 공정 데이터 수집
- 샘플링 데이터(온도, 압력, 두께 등) 수집
- 통계적 분석
- 평균(mean), 표준편차(σ), 공정 능력 지수(Cp, Cpk) 등을 계산
- 제어도(Control Charts) 활용
- X̄-R Chart, X̄-S Chart, P-Chart 등으로 공정 이상 감지
- 공정 이상 감지 및 조치
- 이상 발생 시 원인 분석 후 공정 조정
적용 예
- 반도체 웨이퍼 두께의 평균 및 변동을 감시하여 공정 이상 탐지
- PCB 기판 제조에서 솔더 페이스트 도포 두께 관리
3. FDC와 SPC의 차이점 및 활용
구분 | FDC (Fault Detection & Classification) | SPC (Statistical Process Control) |
---|---|---|
목적 | 공정 이상 감지 및 원인 분석 | 공정 변동 감시 및 품질 관리 |
방법 | 센서 데이터 분석, 머신러닝, 패턴 인식 | 통계적 기법(X̄-R Chart, Cp/Cpk 분석 등) |
적용 분야 | 반도체 장비, 공정 이상 탐지 | 품질 관리, 공정 최적화 |
결과 | 이상 발생 시 원인 분석 및 대응 | 품질 변동을 최소화하여 안정적인 생산 유지 |
4. FDC + SPC 통합 활용
- FDC는 이상 감지 및 원인 분석에 초점, SPC는 장기적인 품질 관리에 초점
- 두 기법을 함께 사용하면 실시간 이상 감지 + 장기적인 품질 관리가 가능
예제 시나리오 (반도체 공정)
- SPC로 공정 데이터 모니터링 → 공정 변동이 증가하면 경고
- FDC로 원인 분석 → 특정 장비 센서 값 이상 감지
- 대응 조치 → 장비 유지보수 또는 공정 조건 최적화
FDC 적용 사례: PECVD(Plasma Enhanced Chemical Vapor Deposition) 공정
📌 상황:
PECVD 장비는 웨이퍼 위에 절연막(실리콘 산화물, 질화막 등)을 증착하는 장비입니다. 이 과정에서 가스 유량, 챔버 압력, 플라즈마 파워 등의 변수가 매우 중요한데, 작은 이상이 발생해도 증착 균일도가 떨어져 불량이 발생할 수 있습니다.
✅ 적용된 FDC 기법
- 센서 데이터 수집: 챔버 내부의 온도, 가스 유량, 압력, 플라즈마 파워 등 실시간 모니터링
- 머신러닝 기반 이상 감지: 정상 공정 패턴과 비교하여 특정 변수(예: 가스 유량 급격한 변화)가 발생하면 이상 감지
- 이상 원인 분석
-
- 가스 유량이 정상보다 낮아졌다면 Mass Flow Controller (MFC) 고장 가능성
- 플라즈마 파워 변동이 심하면 RF 전원 불안정 문제
- 챔버 압력이 비정상적으로 높다면 펌프 시스템 이상
🎯 결과
- 이상 감지 후 즉시 공정을 중단하여 불량 웨이퍼 생산 방지
- 장비 유지보수 예측(Predictive Maintenance) 가능
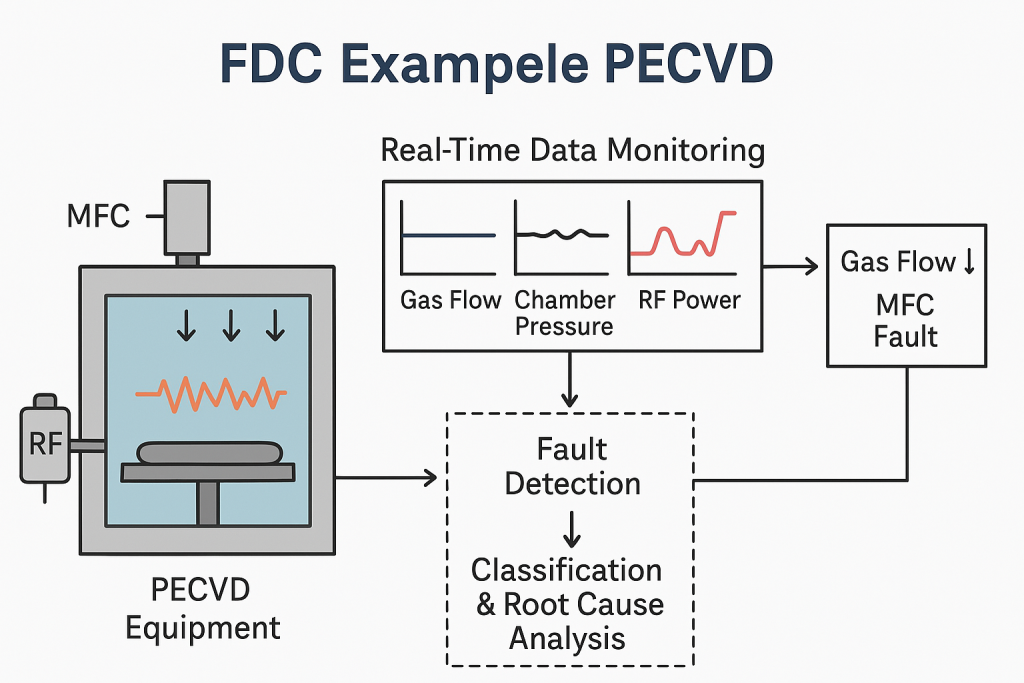
SPC 적용 사례: CMP(Chemical Mechanical Planarization) 공정
📌 상황
CMP 공정은 웨이퍼 표면을 평탄화하는 과정으로, 슬러리(연마액) 공급량, 패드 상태, 압력 등이 품질에 큰 영향을 미칩니다.
공정 중 변수가 일정 범위를 벗어나면 불량률이 급증할 수 있습니다.
✅ 적용된 SPC 기법
- 제어도(Control Chart) 분석
- 웨이퍼 두께 변화를 X̄-R Chart로 모니터링
- Cpk(공정 능력 지수) 분석을 통해 공정이 정상 범위 내 유지되는지 확인
- 공정 이상 탐지
- 평균 두께가 점진적으로 줄어드는 패턴을 보이면 슬러리 공급량 감소 문제 가능성
- 특정 로트에서 두께 편차가 커지면 패드 마모 심화 가능성
- 대응 조치
- 슬러리 공급 시스템 점검 및 조정
- 패드 교체 주기 조정
🎯 결과
- 공정 변동이 심해지기 전에 사전 대응 가능
- 웨이퍼 두께 균일도를 개선하여 불량률 감소

제어 한계(Control Limits)를 설정하여 이상 여부를 판단
FDC + SPC 통합 적용 사례: Etch(식각) 공정
📌 상황
반도체 식각 공정에서는 플라즈마를 이용해 웨이퍼 표면의 특정 영역을 제거합니다.
공정 변수(플라즈마 파워, 가스 유량, 챔버 압력 등)가 미세하게 변해도 식각 깊이가 달라져 불량이 발생할 수 있습니다.
✅ 통합된 FDC & SPC 기법
- SPC로 공정 모니터링
- 웨이퍼 식각 깊이 데이터를 X̄-S Chart로 분석하여 이상 변동 감지
- 공정 능력 지수(Cpk)가 감소하면 공정 변동성이 증가한 것으로 판단
- FDC로 원인 분석
- 식각 깊이가 점점 얕아지는 경우 → 플라즈마 파워 저하 가능성
- 특정 웨이퍼에서만 깊이가 다르면 → 가스 유량 불안정 문제
- 대응 조치
- 플라즈마 파워 소스 점검 및 유지보수 수행
- 가스 유량 조절 밸브 교체
🎯 결과
- FDC를 활용하여 이상 감지 및 신속한 원인 분석
- SPC를 활용하여 장기적인 공정 품질 유지
FDC와 SPC를 함께 적용하면?
- FDC: 실시간 이상 감지 및 원인 분석 → 즉각적인 조치 가능
- SPC: 장기적인 공정 변동 감시 및 품질 유지 → 공정 안정성 확보
-
결과적으로 반도체 공정의 수율을 높이고 불량률을 낮추는 데 필수적인 기술이 됩니다.
😊 SPC(Statistical Process Control, 통계적 공정 관리)에서 X̄-R Chart, X̄-S Chart, P-Chart 등은 공정 데이터를 분석하여 이상 여부를 감지하는 대표적인 제어도(Control Chart)입니다. 각각의 차트가 어떤 원리로 공정 이상을 감지하는지 설명하겠습니다.
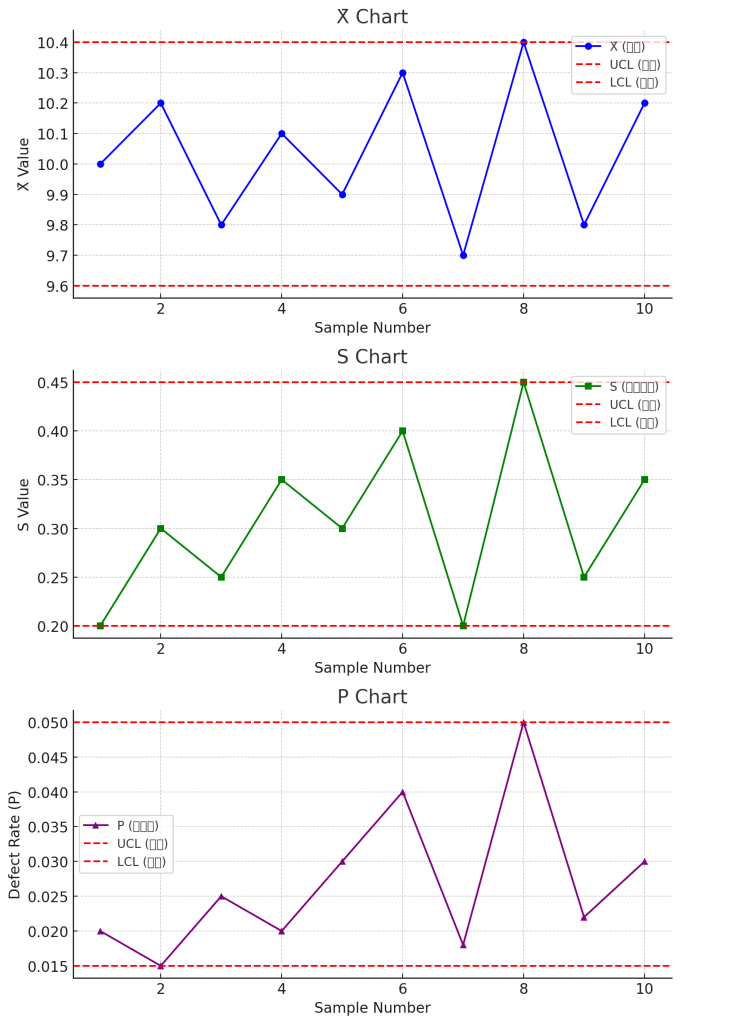
- X̄ Chart: 샘플 평균(X̄)의 변화를 보여주며, 상한(UCL)과 하한(LCL)을 벗어나면 공정 이상을 감지합니다.
- S Chart: 샘플의 표준편차(S) 변화를 감시하여 공정 변동성을 분석합니다.
- P Chart: 불량률(P)이 기준 한계를 초과하는 경우 공정 이상으로 판단합니다.
1. X̄-R Chart (X바 – R 관리도)
📌 개요:
- X̄(엑스바) Chart: 샘플 그룹의 평균을 추적
- R(Range) Chart: 샘플 그룹의 범위(최대값 – 최소값) 를 추적
- 주로 소규모 샘플(2~10개) 로 공정 변동성을 감시할 때 사용
✅ 공정 이상 감지 원리:
- X̄ Chart 분석
- 중심선(CL, Central Line): 샘플 평균의 장기적인 평균
- 상한 관리 한계(UCL, Upper Control Limit), 하한 관리 한계(LCL, Lower Control Limit)
- 샘플 평균이 UCL/LCL을 벗어나면 공정 이상 발생
- R Chart 분석
- 개별 샘플 내 변동성이 너무 크면 공정 불안정 신호
- R 값이 갑자기 커지면 계측기 오작동 또는 공정 이상 가능성
🎯 적용 예제 (웨이퍼 두께 관리)
- 5개의 웨이퍼 두께를 샘플링하여 평균과 범위를 기록
- 평균 두께가 서서히 줄어들면 증착 공정의 가스 유량 이상 가능성
2. X̄-S Chart (X바 – S 관리도)
📌 개요:
- X̄ Chart: 샘플 그룹의 평균을 모니터링
- S(Standard Deviation) Chart: 샘플의 표준편차(σ, Standard Deviation) 를 모니터링
- 샘플 크기가 클 때(10개 이상) 사용
- R Chart보다 정밀한 변동성 분석 가능
✅ 공정 이상 감지 원리:
- X̄ Chart 분석 → 샘플 평균이 점점 이상 범위로 벗어나는지 확인
- S Chart 분석 → 표준편차(σ)가 일정 범위를 벗어나면 공정 변동 증가
🎯 적용 예제 (포토리소그래피 패턴 크기 관리)
- 웨이퍼 패턴 크기를 15개씩 샘플링하여 X̄-S 관리도 작성
- 표준편차(S) 값이 점점 커지면 공정 불안정 → 노광 장비 초점 이상 가능
3. P-Chart (비율 관리도, Proportion Chart)
📌 개요:
- 불량품 비율을 추적하는 제어도
- 제품이 합격/불합격(양품/불량품)으로 구분되는 경우 사용
- 샘플 크기가 일정하지 않아도 적용 가능
✅ 공정 이상 감지 원리:
- 불량률 계산 → 주기적으로 샘플을 검사하고 불량 비율 계산
- UCL/LCL 설정 → 기준을 벗어나면 공정 이상
- 점진적인 증가 감지 → 특정 로트에서 불량률이 증가하면 공정 문제 가능
🎯 적용 예제 (반도체 패키징 검사)
- 하루에 100개의 반도체 칩을 검사하여 불량 비율을 기록
- 특정 날짜 이후 불량률이 급증하면 장비 세정 문제 가능
비교 요약
제어도 종류 | 분석 대상 | 사용 조건 | 적용 예제 |
---|---|---|---|
X̄-R Chart | 샘플 평균 & 범위 | 소규모 샘플(2~10개) | 웨이퍼 두께, 금속 증착량 |
X̄-S Chart | 샘플 평균 & 표준편차 | 대규모 샘플(10개 이상) | 포토리소그래피 패턴 크기 |
P-Chart | 불량품 비율 | 합격/불합격으로 구분되는 제품 | 반도체 패키징 검사 |
🔥 결론: 어떻게 활용하면 좋을까?
- X̄-R Chart → 공정이 안정적인지 빠르게 판단
- X̄-S Chart → 공정 변동성이 높은 경우 정확한 분석 가능
- P-Chart → 불량률을 모니터링하여 장기적인 품질 개선